Introduction
Chemicals have many benefits in the present day society and our contemporary life is completely dependent on them (1). Today, thousands of chemicals are used all over the world (2). Workplace chemical contaminants include gases, vapors, and solid or liquid suspended particles. Each of these materials has specific risks, and the effects caused by these materials differ depending on the type of chemical, route of entry, duration, and density. Excessive exposure to these materials at work can cause poisoning and a variety of diseases (3, 4). Some consequences of exposure to chemicals are instantaneous, but since many of the chemicals are used in low concentrations or the rate of exposure is low, the effects of exposure are cumulative and will appear in the body over a long period of time. Therefore, certain systemic symptoms may not occur in the short term and symptoms are observed in the long term and they have consequences such as illness, motion or physical injury, and even death (5). The number of factories producing chemicals has increased significantly and new products are introduced into the market each year. Consequently, the number of employees at risk of exposure to these materials has also increased. Some of these chemicals are new compounds and mixtures and their toxicological properties have not been studied previously and they may be dangerous to humans (6). The World Health Organization (WHO) statistics indicate that 4 million people worldwide are engaged in the chemical industry, and 1 million people die or are disabled annually as a result of unsafe exposure to chemicals (7).
The petrochemical industry is one of the important industries that have a major effect on the country's economic growth. Petroleum products and raw material required for numerous processes in many other industries are produced in this industry. Therefore, workers are exposed to various contaminants. The need for a comprehensive plan to determine hazardous chemicals that effect the health of individuals exposed to these materials and also hazardous tasks and processes can be felt today more than ever (6, 8). This can be achieved through chemical risk assessment. Chemical risk assessment can assist in the prioritization of hazardous contaminants, and the selection of appropriate control measures (9). In other words, the risk assessment of chemicals can be a comprehensive assessment of workers’ exposure to health risk factors and decisions about anticipated control measures, training of employees, monitoring, and health care to protect employees against exposure to hazardous chemicals in the workplace (10). There are several methods for risk assessment, but methods that are able to assess sanitary risks caused by exposure to chemicals are rarely considered.
In quantitative methods, epidemiological data is used for assessing sanitary risks. An example of this is the study of Jafari et al. in which the relative risk of leukemia due to benzene exposure was calculated. In qualitative methods, employees’ rate of exposure to occupational hazardous factors is estimated through determining the degree of risk and exposure using a risk assessment matrix (8, 11). Due to the lack of national epidemiological data and the long duration of quantitative methods, a specific and functional method for risk assessment of occupational exposure to harmful chemical agents was introduced in this study. Furthermore, we used this method in the petrochemical industry to determine the exposure level to chemicals and prioritize control measures to reduce risks to an acceptable level.
Material and Methods
This study was conducted in the operation unit of an Iranian petrochemical company that has the most variety of pollutants and its workers are exposed to high levels of pollutants.
In total, 24 tasks were examined in this study and ultimately risk assessment was performed for 19 hazardous chemical substances. This study was conducted through census method; thus, there was no need to determine the sample size.
The method of sanitary risk assessment of hazardous chemical agents in the work environment provided by the Department of Occupational Health in Singapore was used in this study (12). This approach was implemented in the following steps:
- Formation of working groups: The members of this working group consist of the supervisor of the operations unit, an employee representative, an employer representative, and an occupational health or safety specialist.
- Analysis of the process of operations into smaller tasks: At this stage, operations unit workers were grouped according to their occupational tasks, and then, the tasks of each occupation was analyzed.
Table 1: Determination of the degree of risk through the toxic or harmful effects of chemicals
Risk degree |
Description of the effects of chemicals in the division of chemical hazards |
Example |
1 |
Substances that do not have any known health effects and have not been classified as toxic or harmful
Substances that have been categorized as group A5 (not suspected as a human carcinogen) by the ACGIH |
Sodium chloride, calcium carbonate |
2 |
Materials that have reversible effects on the eyes, skin, and mucous membranes, but their effects are not severe enough to cause serious damage to human beings
Substances that the ACGIH has categorized as group A4 (not classifiable as a human carcinogen) |
Acetone, butane, acetic acid |
3 |
Substances that are possibly carcinogenic or mutagenic to humans or animals, but there is not enough information about cancer-causing substances that the ACGIH has categorized as group A3 (confirmed animal carcinogen with unknown relevance to humans). |
Toluene, xylene, ammonia |
4 |
Substances that may be carcinogenic, mutagenic, and teratogenic according to studies carried out on animals
The number of these substance are more than the previous category
Substances that the ACGIH has categorized as group A2 (suspected human carcinogen). |
Formaldehyde, cadmium, methylene chloride |
5 |
Substances known for their carcinogenic, mutagenic, and teratogenic effects
substances that have been categorized by the ACGIH as group A1 (confirmed human carcinogen) |
Benzene, lead, arsenic |
ACGIH: American Conference of Governmental Industrial Hygienists
- Identification of chemicals: At this stage, all chemicals (including general, intermediates, products, and by-products) that were produced or consumed during the process were identified. All materials in the form of solid, liquid, gas, vapor, mist and fume dust were examined. In this study, basic instructions, process flow diagrams, and process and instrument diagram (P&ID) were used to identify chemicals.
- Determination of the degree of risk: Tables 1 (determination of chemical safety) and 2 were used to determine the toxicity of materials.
Table 2: Determination of the degree of risk using the acute toxicity of chemicals
LD50 absorbed orally (mg/kg body weight of rats) |
LD50 absorbed through the skin (mg/kg body weight of rats) |
LD50 absorbed through inhalation in rats (mg/l gases and vapors in 4 hours) |
LD50 absorbed through inhalation in rats (mg/l, aerosols and particulate matter in 4 hours) |
Degree of risk |
LD50 > 2000 |
LD50 > 2000 |
LC50 > 20 |
LC50 > 5 |
2 |
200 < LD50 < 2000 |
400 < LD50 < 2000 |
2 < LC50 < 20 |
1 < LC50 < 5 |
3 |
25 < LD50 < 200 |
50 < LD50 < 400 |
0.5 < LC50 < 2 |
0.25 < LC50 < 1 |
4 |
LD50 < 25 |
LD50 < 50 |
LC50 < 0.5 |
LC50 < 0.25 |
5 |
5. Determination of the degree of exposure (ER) with the exposure index (EI:( In this study, considering that air monitoring results (measurement results of exposure) were not available, the degree of exposure was calculated with theEI according to the following formula:
ER=[EI1×EI2×EI3×……EIn]1n
where n is the number of used exposure factors.
The EI was obtained based on a numerical scale (1 to 5; 1 = very low, 3 = medium, and 5 = very high) using table 3.
Table 3: Determination of exposure index
5 |
4 |
3 |
2 |
1 |
Exposure index |
Exposure factor |
More than 100 mmHg, Powder, dry and fine particles
Less than 10 micrometers |
10-100 mmHg
Fine and dry materials Between 10 and 100 micrometers |
0.1-10 mmHg Fine and dry particles
More than 100 micrometer |
0.1-1 mmHg Fine and dry particles |
less than 0.1 mmHg
Coarse particles and wet material |
Vapor pressure or particle size in terms of aerodynamic diameter |
2 < |
1-2 |
0.5-0.99 |
0.1-0.49 |
< 0.1 |
Ratio of olfactory threshold to permissible exposure limit |
Without any control (very high level of dust) |
Inadequate control (much dust) |
Adequate control and maintenance (dust average) |
Adequate control with regular maintenance |
Adequate control with regular maintenance |
Control measures |
- High usage rate
- Workers have not been trained to work with chemicals
- More than 1000 kilograms or liters |
High usage rate
- Workers have been trained to work with chemicals
- 10-1000 kilograms or liter |
Average amount of use
- Workers have been trained in the transportation of chemicals
- 1-100 kilograms or liters |
low amount of use
- 1-10 kilograms or liters
|
Negligible amount of use
- Less than 1 kilogram or liter
|
Amount of material used per week |
32-42 hours |
32-42 hours |
16-24 hours |
8-16 hours |
Less than 8 hours |
Working time per week |
In the above table, when the chemical is in liquid form at room temperature, the risk of exposure to it depends on its vapor pressure, which can be obtained from the material safety data sheets (MSDS).
In the case of one solid chemical substance, the risk of respiratory exposure depends on the size of the solid particles. The particle size can be obtained by calculating the aerodynamic diameter of particles using the following equation:
Da=Dp2s.g
where Dp is the particle diameter, Da is the aerodynamic diameter and s.g the density.
Moreover, the level of exposure to a chemical substance in the fourth and fifth rows of the above tables depends on the amount and duration of exposure. In this study, 1 week work period (usually 40 hours) is considered as the basis for determining the exposure factor.
- Risk assessment: At this stage, according to the hazard rate (HR) and exposure rate (ER) of chemicals, the risk was obtained using the following equation. It should be noted that in this study, when the level of calculated risk was not a whole number, it was rounded up to the nearest whole number.
Risk level=HR×ER
- Rating of risk: The risk of occupational exposure to chemicals in each task was ranked using the risk level and the ranking of risks were as follows:
- Risk level 1: Small–negligible
- Risk level 2: Low
- Risk level 3: Medium
- Risk level 4: High
- Risk level 5: Very high
The following matrix used to determine the level and rank of risk (Table 4).
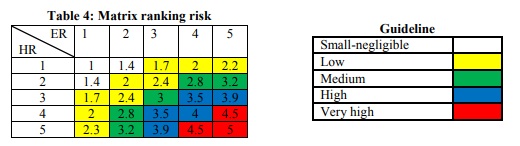
Results
This study was performed on 95 employees working in the operation unit of a petrochemical company. In this study, the mean and standard deviation of age of participants was 30.28 ± 7.87. The mean and standard deviation of their work experience was 5.98 ± 5.66. Moreover, 25.3% of the participants were single and 74.7% married. As can be seen in table 7, there were significant differences between the mean age and job tenure of individuals at low and high risk.
Table 5 is presents the ranking of risk in Job tasks of the PX (P-xylene) process in unit 400. As can be seen in table 5, the highest risk was related to work with benzene with risk level 4. Other tasks were exposed to chemicals with risk level 3.
Table 5: Ranking of risk in Job tasks of PX (P-xylene) process in unit 400
Risk level |
Exposure rate |
Hazard rate |
Chemical |
Task |
Row |
3 |
3.1 |
3 |
Xylene |
Washing of unit equipment |
1 |
3 |
2.2 |
3 |
Xylene |
Sampling of products as an example
|
2
|
3 |
2.2 |
3 |
Toluene |
4 |
2.2 |
5 |
Benzene |
3 |
2.2 |
3 |
Xylene |
Routine replacement of pumps for lower equipment depreciation |
3 |
3 |
2.2 |
3 |
Xylene |
Opening and shutting of valves |
4 |
3 |
2.2 |
3 |
CO |
Inspection of the furnace in service |
5
|
3 |
2.2 |
3 |
H2S |
4 |
2.2 |
5 |
Benzene |
Substitution of KLAY DRAM |
6
|
4 |
4.4 |
3 |
Xylene |
Table 6 presents the risk ranking in Job tasks of the PX process in unit 700-800. As listed in table 6, the tasks include replacing of ammonia cylinders, Inspection of the state of the PDEB (Para diethylbenzene), cleaning of equipment, inspection and replacement of nitrogen cylinders in the absorption tower (tower 8801 and related reflux drum), inspection of the operation of compressors turbine, sampling of products as an example, inspection of fans, routine replacement of pumps for lower equipment depreciation, purification of PDEB solvent in T-7005 towers, and inspection of the state of the furnace in service. In this unit, all tasks had a level 3 risk, except the inspection of fans and replacement of pumps that had a level 2 risk.
Table 7 presents the tasks of the PX process in unit 950; the lowest risk level was 2 and the highest was 3. The amount of risk level is illustrated in figure 1. In this study, 72%, 19%, and 9% of risk was at a medium, low, and high level.
Table 6: Risk ranking in Job tasks of PX (P-xylene) process in unit 700-800
Risk level |
Exposure rate |
Hazard rate |
Chemical |
Task |
Row |
3 |
3.4 |
3 |
Ammonia |
Replacement of ammonia cylinders in unit 800 |
1 |
3 |
3 |
3 |
Para diethylbenzene |
Inspection of the state of the PDEB (Para diethylbenzene) |
2 |
3 |
2.6 |
3 |
Xylene |
Cleaning of equipment |
3 |
2 |
1.7 |
1 |
Nitrogen |
Inspection and replacement of nitrogen cylinders in the absorption tower |
4 |
3 |
2.1 |
3 |
H2S |
Inspection of Tower 8801 and related reflux drum |
5 |
3 |
2.1 |
3 |
H2S |
Inspection of the operation of the turbine compressors |
6 |
3 |
2.5 |
3 |
H2S |
Sampling of products as an example |
7 |
2 |
2.1 |
1 |
CH4 |
Inspection of fans |
8 |
2 |
2.6 |
1 |
C1-C4 |
Routine replacement of pumps for lower equipment depreciation |
9 |
3 |
2.6 |
3 |
CO |
3 |
3 |
3 |
Para diethylbenzene |
Purification of PDEB solvent in T-7005 towers |
10 |
3 |
2.5 |
3 |
H2S |
Inspection of the state of the furnace in service |
11 |
Table 7: Risk ranking in tasks of the PX process in unit 950
Risk level |
Exposure rate |
Hazard rate |
Chemical |
Task |
Row |
3 |
2.1 |
3 |
H2S |
Deaeration of pumps |
1
|
2 |
2.1 |
1 |
CH4 |
3 |
3.4 |
2 |
Chemical 1044 |
Cleaning of equipment |
2 |
3 |
2.5 |
3 |
H2S |
Inspection of the operation of the turbine compressors |
3 |
2 |
2.2 |
1 |
C1-C5 |
Sampling of products as an example |
4 |
2 |
1.5 |
2 |
Grace |
Inspection of fans |
5 |
3 |
2.4 |
2 |
Oil |
Routine replacement of pumps for lower equipment depreciation |
6 |
3 |
2.2 |
3 |
H2S |
Inspection of the state of the furnace in service |
7 |
3 |
2.2 |
3 |
CO |
Discussion
In this study, workers were exposed to 19 chemicals during the performance of their duties. Among these materials, benzene and xylene had the highest risk. These two chemicals were present in the tasks of sampling of products as an example, cleaning of the unit equipment, replacement of pumps, opening and shutting of valves, and inspection of drum reflux. This study showed that Xylene have higher risk level in job task of PLAY DRAM replacement compared to other tasks. Das it have priority to reduce through modification of task and use of appropriate protective equipment.
Benzene with is a high-risk (number 5) chemical and has toxic effects. However, given the low exposure levels (2), a control measure was established based on the reduction of exposure to this material to reduce the degree of exposure to rating 1.
In the study by Malakooti et al., no significant relationship was found between risk of chemicals in laboratory workers and marital status (13). Nevertheless, in the study by Ghods et al. conducted to investigate the epidemiology of occupational accidents in Semnan, it was found that 63% of accidents occur among married employees. As mentioned above, the results of this study showed a significant relationship between risk and marital status (P < 0.015) (14).
The results showed that experience and age affected the risk level. Several studies have reported the prevalence of accidents in individuals with low experience (15-18). Thus, we can conclude that occupational history and experience is effective in reducing exposure to chemicals. In this study, no relationship was observed between the level of education and risk level. This was also observed in the study by Kingdom et al. on risk assessment of chemicals in the laboratory (13).
This study had some limitations, including that some of the chemicals that existed in the investigated industry were not listed on the MSDS, so it was not possible to assess them. Another limitation of this study was that micromaterials and nanomaterials that are not identifiable through the available methods and tools may be present in companies. Since there is no regular program in the country to assess and prioritize chemicals in industries, the use of this method is proposed as a systematic assessment method for evaluating chemicals and prioritizing strategies to control chemicals.
Conclusion
It can be concluded from this study that 81% of chemicals used in the studied industry were rated as moderate and high risk. In order to control the identified risks, programs and control measures are recommended based on the hierarchy of elimination, substitution, engineering control, administrative control, and use of personal protective equipment.
Acknowledgments
The authors are grateful to the faculty members of the Department of Occupational Health and all managers and staff of the studied petrochemical plant for their cooperation in this project.
Conflict of interests: None declared.